Reduced Batch Stones
The combination of faster melting and lower temperature dissolution of silica grains when using Calumite Slag can result
in a reduction in batch stones without the need to increase furnace temperature. Figure 4.3 shows how the implementation
of Calumite Slag in a float furnace led to the virtual elimination of unmelted silica defects.
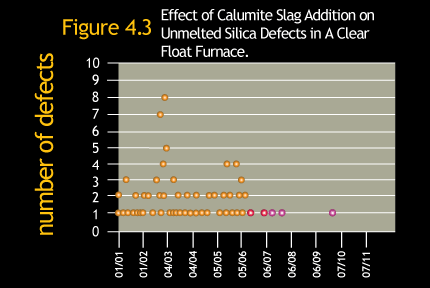
Color Stabilization
Calumite Slag is particularly valuable in the production of amber glass, or glass with an amber component to their color,
such as dead leaf green or UVA green. The amber chromophore that produces the color in these glasses consists of reduced
sulfur in the form of sulfide, S2-, combined with the oxidized form of iron, Fe3+. Calumite Slag can be used to control
redox such that the reduced sulfur and oxidized iron can co-exist.
Reduced Refractory Attack
The reduction in furnace temperature that can be achieved while using Calumite Slag will reduce the level of refractory
attack, directly reducing the number of defects, e.g. due to refractory run off. This reduced refractory wear will also
have significant additional benefits in terms of extending furnace campaign life.
Improved Redox Control
Calumite Slag is a weak reducing agent when compared to reducing agents such as carbon. As a result, comparatively large
amounts of Calumite Slag are added to the recipe, resulting in more even distribution within the batch. In addition, the
larger particle size of Calumite Slag compared to other reducing agents ensures the material is available to react over
a longer period of time.
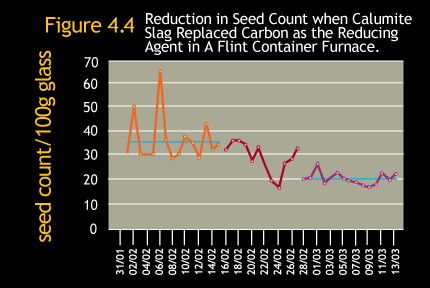